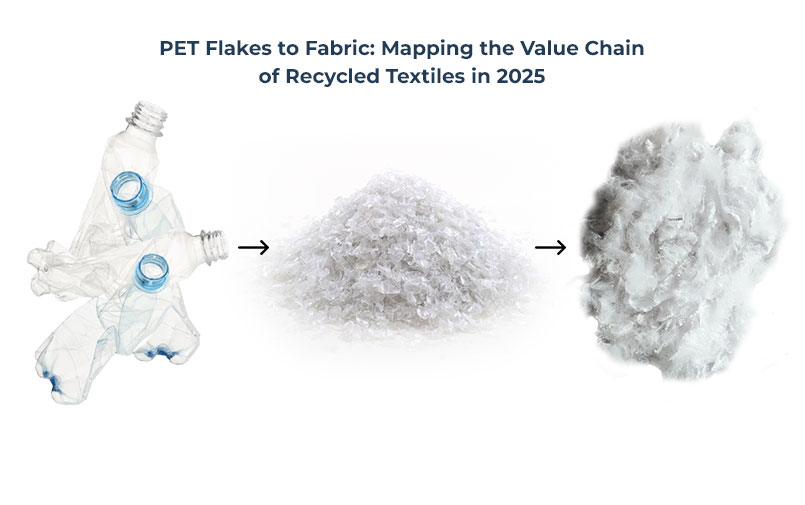
A few years ago, sustainability felt like a choice. In 2025, it feels more like a responsibility. Especially in textiles, where every input is being examined more closely than ever.
At JB Ecotex, we’ve spent the last decade working with what the world throws away. A bottle discarded in one city finds its way into a yarn spool thousands of miles away. What used to be packaging is now padding. What used to be seen as trash is now woven into stories brands can be proud of.
This is what PET flakes recycling has made possible – not just technical progress, but material narratives that reflect intent, accountability, and change.
The Start of the Journey: Bottles Become Raw Material
The value chain begins with something simple: a used PET bottle. From consumer bins to collection centers, these bottles move through sorting systems designed to isolate clean, usable material.
Once selected, they are washed, shredded, and dried to create clear, consistent PET flakes – the feedstock for the next phase. This process may sound routine, but in 2025, it’s where some of the most important quality control work happens.
Clean, food-grade-compliant flakes enable smoother downstream processing. For manufacturers, this stage ensures they can move toward recycled textiles India projects without production setbacks.
From Flakes to Fibre: The Plastic to Fabric Process
Flakes enter the melt spinning phase, where they are transformed into recycled polyester staple fibre (RPSF). After extrusion and cutting, these fibres resemble cotton in texture but perform like polyester.
It’s in this moment that the material crosses over – from waste to textile-ready fibre. The plastic to fabric process has taken something previously discarded and prepared it to be sewn, stretched, or stuffed.
Applications vary widely: soft knits, filling fibres, and industrial textiles all rely on this transition.
Why It Matters to Manufacturers in 2025
Textile production teams aren’t just looking for sustainability language. They are looking for fibres that perform reliably and integrate smoothly with their current systems.
This is where RPSF holds relevance. Manufacturers come to us with specific goals – whether it’s sourcing eco-friendly polyester fibre for a sustainability-conscious collection or substituting a portion of virgin raw material in fillings and padding.
They ask questions like:
1. Can this fibre spin cleanly?
2. Will it match dye absorption across batches?
3. How does RPSF vs virgin fibre compare in tensile strength?
These are not philosophical questions. They are production-level realities, and the material has to rise to meet them.
Increasingly, we are seeing RPSF discussed in the context of sustainable textiles procurement strategies. Buyers are factoring recycled content into sourcing decisions, both for performance value and compliance needs.
Where Recycled Polyester Is Being Used in 2025
We are seeing recycled PSF for spinning used across:
1. Fashion basics and daily-wear apparel
2. Cushion and pillow fillings for home and hospitality
3. Nonwoven rolls used in industrial and filtration markets
4. Automotive linings and seat fabrics
In each case, the demand is not just for performance. It is for traceability, stability, and a lower environmental profile.
More international buyers are now working only with GRS certified RPSF suppliers in India to ensure their own compliance goals are met. This growing shift continues to position RPSF India as a reliable sourcing destination.
JB Ecotex’s Process: From Flake to Fibre
At JB Ecotex, our PET flakes are sourced from post-consumer bottles and washed in a multi-stage system designed to ensure high clarity and cleanliness. We monitor moisture levels, contaminants, and label residues.
The goal is not to compete with virgin fibre. It is to support an alternative that meets your needs while aligning with modern sourcing strategies.
Our recycled polyester staple fibre is used by clients across apparel, nonwoven, automotive, and filling categories. Documentation, sample support, and batch-level specs are shared as needed.
What Comes Next: Textile Waste to Fiber
While PET flakes recycling begins with bottles, industry leaders are now looking at textile waste as the next major resource. In India and beyond, post-industrial and post-consumer fabric waste is being explored as feedstock for the next generation of recycled fibres.
This textile waste to fiber movement reflects the broader ambition to create circular ecosystems, not just recyclable products. As sorting systems, mechanical processes, and partnerships evolve, more waste streams may become usable inputs. At JB Ecotex, we remain aligned with this direction, watching developments while strengthening our core flake-based processes.
Common Buyer Questions We Hear
1. Can we use this for export-ready production?
Yes, many of our customers prepare materials for international clients. We support with documentation aligned to export expectations.
2. Is this fibre suitable for spinning?
Yes, especially in blends. Many spinning partners work with our fibre for a range of count and blend requirements.
3. How consistent is colour and feel?
We maintain repeatability across batches by managing feedstock quality and melt flow. Customers are encouraged to trial for best alignment.
The Larger Picture: Recycled Textiles and the Future
The global market is shifting. Buyers want clarity about where materials come from. Governments are introducing stricter policies around plastic waste. Consumers are supporting products that feel better because they do better.
In this context, PET flakes recycling is no longer a back-end process. It is a front-of-label story.
Reports from consulting groups like McKinsey confirm that textile recycling is becoming a global value driver, especially as infrastructure and consumer education improve.
Why PET Flakes Recycling Is Growing in 2025
The interest in PET flakes recycling is being driven by multiple forces. Global brands are re-evaluating material use. Governments are introducing EPR requirements. Consumers are responding to labels that reflect values, not just fashion.
India is among the regions seeing growth in recycled textiles manufacturing. This shift is influencing how fibre is sourced, how products are marketed, and how manufacturers prepare for upcoming regulation.
FAQ
1. What are the benefits of PET flakes recycling for textile manufacturers?
It enables the use of recycled raw material in a wide range of applications and helps respond to increasing market and regulatory expectations.
2. Can recycled PSF for spinning match virgin inputs?
Many textile processes successfully use RPSF, especially in blends. Properties may vary, so testing is important.
3. How is JB Ecotex’s RPSF produced?
It is made using PET flakes from post-consumer bottles, processed with established washing and extrusion techniques.
4. What documentation is available?
Upon request, JB Ecotex provides technical data sheets and test results related to product specifications.
The JB Ecotex Perspective
At JB Ecotex, we don’t think of recycled fibre as a trend. We see it as a transition. It is about improving how things are made by working with what we already have.
We work with manufacturers who want to ask more of their supply chain – who are open to trialing better materials, managing traceability, and meeting evolving demands without compromising their own quality goals.
If that sounds like where you’re headed, we’d love to support your journey.