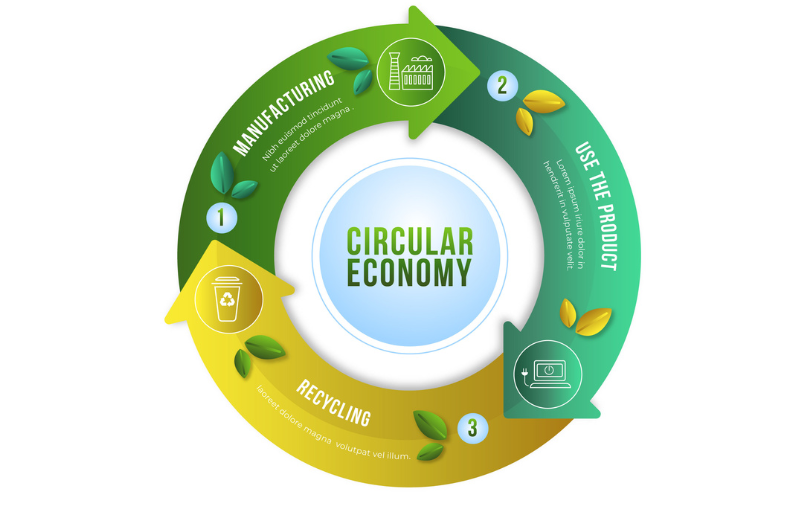
Learn how rPET India is driving the shift to circular packaging. Discover JB ECOTEX’s role in ocean-bound plastic recycling and premium rPET for sustainable supply chains.
Plastic waste is something we’re all familiar with. It’s in our homes, our streets, and too often, our environment. A lot of it comes from packaging—used once and tossed. It doesn’t have to be this way. There are better ways to use materials, and better ways to think about waste. Change starts with reimagining what we throw away.
There is a lot to think about here. Not just about the scale of the problem, but about the opportunity that lies ahead. Packaging is not just where most plastic ends up—it is also where some of the most meaningful change can begin.
This is where food-grade rPET resins come in.
If We Have a Solution, Why Are We Still Complaining
The packaging industry is often blamed for plastic waste. But in many ways, it is also leading the way when it comes to solutions.
Today, we have access to technologies and innovations in PET recycling that can recycle PET bottles and containers into high-quality rPET chips and food-grade B2B rPET resins that can be reused again and again. We can reduce the need for virgin plastic, prevent ocean-bound waste, and build supply chains that are efficient, cost-effective, and sustainable.
And yet, recycled materials like rPET are still underused.
Why? Because the debate on PET vs Virgin Plastic is always raging, and many businesses still view sustainability as a cost rather than an opportunity. Some fear the quality may not match virgin plastic. Others are unsure if switching is worth the effort.
But let’s look at the facts. Recycled polyethylene terephthalate, or rPET, is no longer a weak alternative. It is a robust, scalable, and certified solution that is already powering a shift toward a circular economy across the packaging sector as a recyclable composite material.
What Is a Circular Economy and Why Does It Matter in Packaging
The circular economy is a system where materials are continuously reused, rather than discarded. It stands in contrast to the traditional linear model of take, make, and throw away.
In packaging, circularity means designing systems where plastic does not become waste but is collected, recycled, and reintroduced into new products.
Recycled PET is one of the best materials to support this system. It can be recycled multiple times without major loss in quality, especially when produced and processed correctly.
Where Is rPET Used in the Packaging Industry
PET is one of the most widely used polymers in packaging. Its recycled form, rPET, is now being used in a growing number of high-performance applications.
Here are just a few:
- Food and beverage bottles
- Thermoformed trays and clamshells
- Blister packs and pharma packaging
- PET straps and industrial packaging
- Home care and personal care containers
- Transparent pouches and films
At JB ECOTEX, we supply B2B rPET resins suitable for a range of food-grade packaging applications. Our resins offer excellent transparency, low acetaldehyde levels, and consistent intrinsic viscosity to match industry needs.
Recent Growth and Momentum: The Market is Speaking
You see it more and more. Businesses swapping out regular plastic for recycled stuff. Part of it is pressure from rules, sure, but a lot of it is just people trying to make smarter choices. Materials like rPET are becoming a go-to because they work, and they help cut down on waste. It’s a move in the right direction.
Companies like Unilever and Coca-Cola are leading the way. Coca-Cola has committed to using 50 percent recycled PET in its containers by 2030. Other major global and Indian brands are following suit, knowing that future growth and reputation depend on circularity.
Closer to home, Indian manufacturers are also making the shift, driven by regulatory pressures and rising consumer expectations.
The use of rPET in India is steadily climbing, and suppliers like JB ECOTEX are supporting this movement by offering food-contact-ready resins for a wide range of packaging formats.
What Makes rPET a Circular Material
Not all recycled materials are created equal. But rPET, when processed correctly, stands out for several reasons:
1. High Recyclability
PET can be recycled multiple times with minimal degradation. This makes it ideal for circular systems where the same material can go through many lifecycles.
2. Wide Application Range
rPET is already used in both rigid and flexible packaging, meaning it can replace virgin PET in many common formats without major design changes.
3. Energy and Carbon Savings
Producing rPET requires less energy than producing virgin PET. It also reduces greenhouse gas emissions by around 79 percent.
4. Traceability and Quality Control
With technologies like Erema VACUNITE, rPET can be produced with near-virgin properties. It can be tracked and tested for compliance, making it suitable even for high-precision applications.
Challenges to Circularity and How rPET Addresses Them
While the idea of a circular economy is gaining ground, there are still barriers to adoption.
1. Misconception About Quality
Many manufacturers worry that rPET might be inferior. But today’s advanced processes produce premium rPET that meets performance standards required for even sensitive packaging.
2. Supply Chain Uncertainty
Concerns about sourcing reliable, consistent rPET are valid. That is why manufacturers need partners like JB ECOTEX who provide traceable, verified, and batch-tested material.
3. Regulatory Confusion
Navigating recycled content mandates can be complex. Using rPET helps businesses meet national and industry guidelines, reducing EPR liabilities and preparing for future requirements.
Why rPET is Central to the Circular Economy in Packaging
The packaging industry is in a position of responsibility and influence. What we choose to wrap our products in has a direct impact on the environment, consumer trust, and business resilience.
rPET offers packaging manufacturers a way to reduce plastic waste, meet regulatory targets, and deliver high-quality products to the market. The wise know that sustainability is about being part of a system that works better for everyone.
At JB ECOTEX, we are proud to play a role in this system. With our commitment to plastic recycling, consistent product quality, and support for packaging manufacturers, we are proving that recycled materials can be practical, scalable, and powerful drivers of change.
If you are looking to integrate rPET India into your packaging solutions, we are here to help. Our resins are designed for durability, compliance, and clarity, so you never have to choose between performance and purpose.