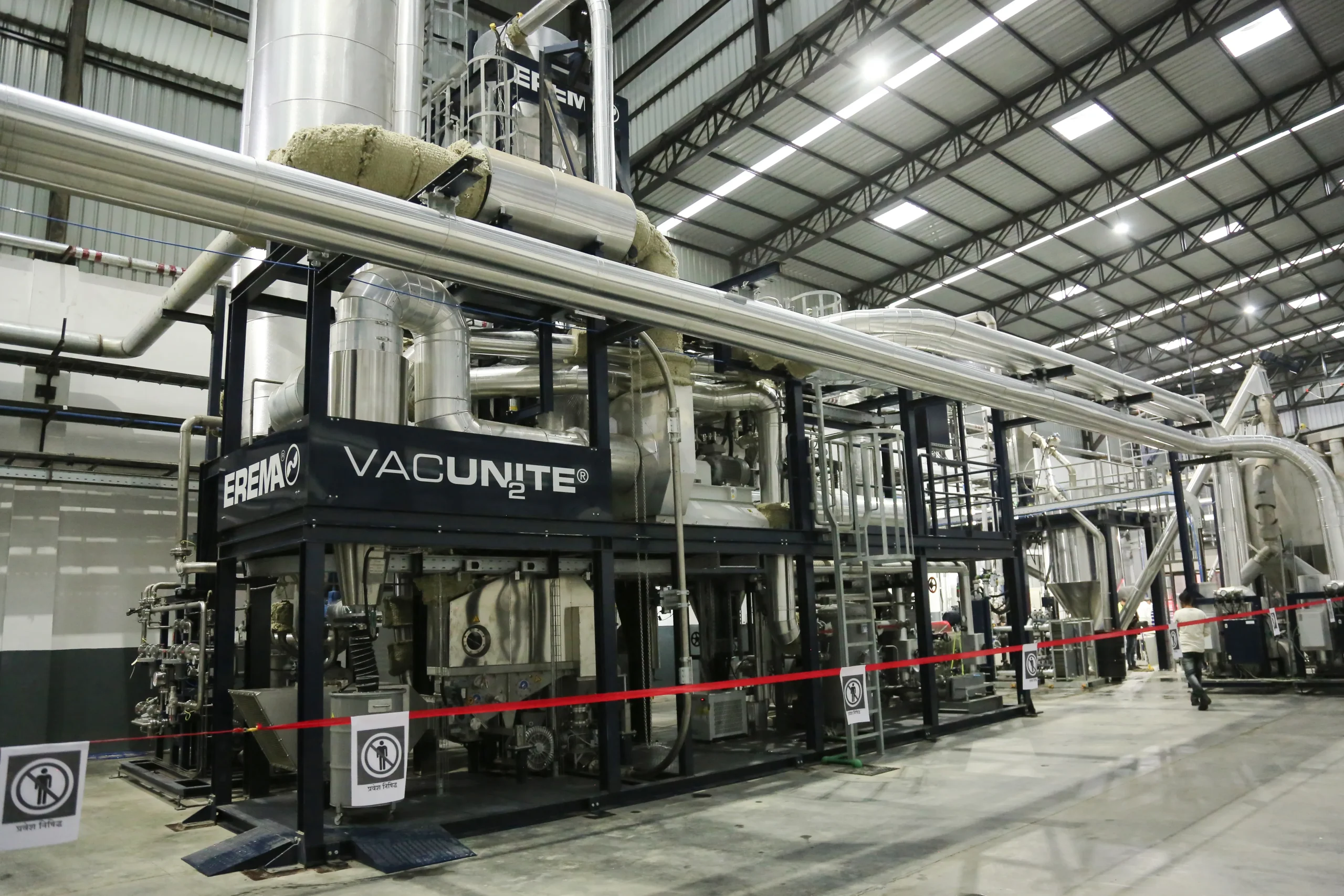
Discover why rPET is a safe choice for food packaging. Learn about JB Ecotex’s advanced recycling methods and EREMA’s innovative VACUNITE® technology, ensuring high-quality, sustainable solutions for a greener future.
The increasing emphasis on sustainability has led to a significant rise in the use of recycled polyethylene terephthalate (rPET), particularly in food packaging. As JB Ecotex Ltd, a prominent manufacturer of mechanical rPET resins in India, we are committed to ensuring that rPET is not only an environmentally friendly option but also a safe one. We hope that by sharing valuable insights we can prove the safety of rPET, highlighting its technical aspects and recent developments that underscore its viability as a sustainable packaging solution.
Understanding rPET and Its Safety
Recycled PET (rPET) resins are produced from post-consumer used water & cold drink bottles which is PET i.e. Polyethylene terephthalate. The safety of rPET, especially for food contact applications, is paramount due to concerns about potential contaminants.
However, rigorous testing and regulatory frameworks ensure that rPET can be safely used in food packaging. Regulatory bodies such as the Food Safety and Standards Authority of INDIA (FSSAI), European Food Safety Authority (EFSA) and the U.S. Food and Drug Administration (FDA) has established stringent guidelines for the use of rPET in food contact materials which ensures suitable quality of rPET resin suitable for food packaging.
Necessary Regulatory Compliance:
As per regulatory bodies, a conventional mechanical recycling process enhanced with an integrated decontamination step such as SSP (Solid state polycondensation) or LSP (Liquid state polycondensation) to remove absorbed contamination through combination of surface treatment high heat and/or high vacuum in an control environment such that output resins are pure enough and having quality parameters as per given guidelines to be used in Food grade packaging.
FG (Food grade) rPET resin produced from the decontamination step should conform with food safety regulatory requirements for virgin PET i.e. level of decontamination shall be below the 220 µg/kg limit in the resin for each surrogate contamination by an extraction test or below the 10 µg/kg limit in the beverage or food simulant for each surrogate contaminate by a migration test. FG rPET also should clear sensory analysis in accordance with ISO13302 or equivalent.
Recent Developments Supporting rPET Safety
In recent years, there has been a notable shift in policy and practice regarding the use of rPET in food packaging:
FSSAI Guidelines: The Food Safety and Standards Authority of India’s (FSSAI) approval of the use of rPET for food applications, facilitating bottle-to-bottle recycling within India, indicates a growing recognition of rPET’s safety and its potential to contribute to a circular economy.
Global Trends: More and more companies are committing to using 100% rPET in their packaging, reflecting a broader trend towards sustainable practices in the industry. These initiatives highlight the increasing consumer confidence in the safety of recycled materials.
These processes ensure that the final product meets the rigorous safety standards set by regulatory authorities, making rPET a reliable choice for food packaging.
rPET Processing: Technical Aspects and precautions
The production of food-grade rPET involves several considerations and precautions that enhance its safety:
Feedstock control & gradation:
As rPET resin are being made up of waste PET bottles, so control & testing of incoming feedstock control is very much important for surety of quality of final rPET resin. As per USFDA, for FG rPET resin production incoming feedstock should have a minimum of 95% used bottles which were used in food packaging.
Extrusion & Decontamination Technology:
Although several extrusion & decontamination technologies are available to make rPET Resin but right set of technology like EREMA VACUNITE® is mandatory to ensure high quality food grade rPET resin.
Quality Control Measures:
Stringent quality control measures on intermediate rPET flakes as well final FG rPET RESINS including in-house testing for analysis of certain VOCs and heavy metals in rPET resin throughout the production at regular intervals make sure the right set of quality of rPET resin which can be used in food packaging.
Companies like JB Ecotex ltd have implemented stringent quality control measures throughout production. Each batch of rPET is tested for various parameters like AA(Acetladehyde), Benzophenone, Limonene and different heavy metals which can migrate with food which will be used for rPET packaging.
FG rPET PROCESS at JB ECOTEX LTD
Technological Advancements Various advanced recycling technologies are able to ensure rigorous decontamination and quality control, producing safe, food-grade rPET. This commitment and confidence among manufacturers enhances consumer trust and supports a sustainable circular economy.
At JB Ecotex Ltd., we utilise the Erema Vacunite technology to manufacture our mechanically recycled PET Resins. EREMA VACUNITE® technology revolutionises bottle-to-bottle recycling by combining advanced VACUREMA® technology with patented vacuum-assisted Solid State Polycondensation (SSP). The same technology is already approved by USFDA & EFSA. This innovative process ensures exceptional decontamination, superior colour quality, and compliance with stringent food safety standards, while also reducing energy consumption by up to 36% compared to traditional systems.
To ensure safety, at JB ECOTEX rPET undergoes several critical processes:
Stringent Quality control of incoming feedstock: JB Ecotex is having strict control over feedstock which is being received at factory and many parameters are being inspected in feedstock to identify feedstock as food grade or non food grade. Feedstock is being stored accordingly.
Washing & Cleaning of feedstock to make rPET Flakes: Advance Hot washing plant equipped with multiple autonomous sorters has been installed to make the required quality of flakes. The bottles are thoroughly cleaned to remove labels, adhesives, and contaminants.
Decontamination with Vacuum reactor followed by extrusion: Material is fed under a constant high vacuum where material is being heated by frictional energy from the slow speed rotating tool. With required heat and vacuum, it works as decontamination of flakes for absorbed impurity which is EFSA approved after a significant challenge test conducted by EFSA.
Followed by initial decontamination, flakes are being melted and filtered to produce rPET RESIN with IV of 0.7.
Decontamination & IV Enhancement (SSP): Advanced techniques such as solid-state polycondensation are employed to remove any absorbed volatile contaminants under the inert environment of Nitrogen. This step is crucial; studies have shown that this process can also effectively reduce potential chemical migration to levels below 0.1 µg/kg food, which is considered safe for human consumption.
Testing Laboratory at JB ECOTEX LTD:
JB ECOTEX group always believes in R&D and rigorous quality analysis for constant improvement of product quality. For manufacturing of rPET Resin company has installed latest testing equipment like Gas chromatography, Inductively Coupled Plasma Mass Spectrometry (ICP-MS), Differential scanning calorimetry (DSC) and many more.
With availability of the latest equipment, the company ensures right quality of FG rPET for safety of users of rPET RESINS.
The future of rPET looks promising as industries as well as consumers increasingly adopt sustainable practices. The India Plastics Pact aims to unite businesses, NGOs, and government entities to enhance recycling efforts and reduce plastic waste. As JB Ecotex continues to innovate in producing high-quality mechanical rPET resins, we remain committed to supporting these initiatives.
At JB ECOTEX with rPET resin manufacturing, our aim is to not only meet regulatory requirements but also cater to environmentally conscious consumers who prioritise sustainability in their purchasing decisions. As more brands recognize the benefits of using safe, recycled materials, we anticipate a significant increase in the adoption of rPET across various sectors.
One can say with confidence that today, the safety of rPET is supported by rigorous testing protocols and regulatory compliance both in India and globally. With advancements in recycling technology and supportive policies from authorities like FSSAI and EFSA, rPET stands out as a safe and sustainable alternative to virgin plastics.
At JB Ecotex Ltd, we are dedicated to leading this charge by providing high-quality mechanical rPET resins that meet international safety standards while contributing positively to our planet’s health. By choosing rPET, industries can play a crucial role in fostering a sustainable future while ensuring consumer safety and confidence.